Manufacturing Paints and Varnishes Using a Powder Disperser
Fumed silica is added to paints and varnishes to adjust the rheology properties and maintain uniform suspension of pigments and additives, which is an advantage for paint and varnish processing. Additional advantages of using fumed silica include promoting adhesion to a variety of surfaces, reducing deterioration rate, hardening, and fading of transparent coatings. Overall, the addition of fumed silica to paints and varnishes ensures a better product quality for the end-user. Fumed silica is a light bulk density, difficult-to-wet hydrophobic powder, preferring to raft on the surface of the mixing vessel.
Powder Dispersion in Paint Manufacturing
The following problems are encountered when introducing difficult-to-wet powders using conventional in-tank mixers:
- Insufficient shear and absence of fluid turbulence results in rafting, tank stratification and production of “fish-eyes” or agglomerates
- Long mixing cycles are necessary to obtain dispersion, uniformity and complete wetting
- Generation of heat due to repetitive shear to incorporate powders can result in the breakdown of pigments and additives
- Mixing difficulties become amplified as fluid viscosity increases, resulting in the inability to develop a vortex to draw the powders into the shear zone of the impeller
- Excess powder build-up on tank walls and mixer shaft, requiring excess cleaning.
Typically, the solution is more equipment to salvage process batch times at the expense of product quality and efficiency.
Quadro's Approach To Manufacturing Paints & Varnishes
The Quadro Ytron® Powder Disperser eliminates these problems through its single-pass technology. Advantages of using single-pass technology include:
- Repeatable and consistent product, batch-to-batch
- One-time, proper application of shear to avoid over-processing high viscosity, shear-sensitive products
- Batch times are typically reduced by 90% - powders can be dispersed during the fill operation of the vessel, thereby reducing batch times
- Elimination of over-processing to eliminate “fish-eyes”
- Less air entrapment, eliminating time to deaerate or requirement to install expensive deaerating equipment
- CIP (Clean-In-Place) design reduces cleaning time and product waste by eliminating powder build-up on batch tank walls and mixer shaft
- Compact size and ease of mobility enable a single disperser to feed multiple tanks.
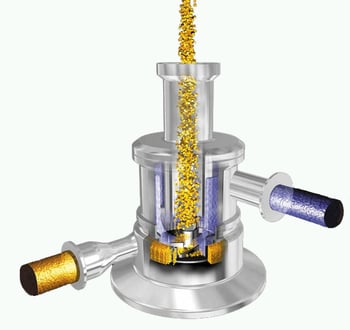
Effective Machinery for Manufacturing Paint
Quadro Ytron® Powder Disperser technology is the ideal choice for adding fumed silica into paints and varnishes. Quadro Ytron® offers tooling in a variety of sizes to create the desired dispersion in-line, in a single-pass. Quadro's customers expect homogeneous products, combined with excellent customer service.
Learn more about Quadro Liquids Mixing Equipment for Chemicals via our Industries page.
Topics:
Powder Dispersion